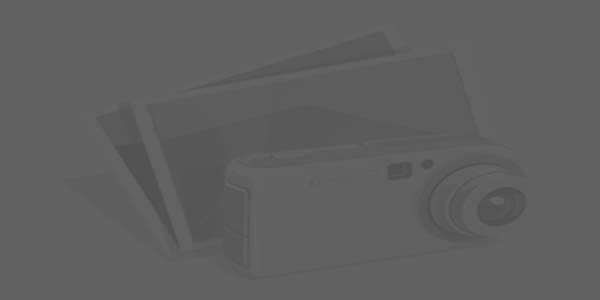
Part 6
Chapter IX.
SPOONS, SUGAR TONGS AND TEA SCOOPS.
These exercises are easily carried out after a little experience. No steps are taken that have not already been described, except in the case of forming the bowl of the spoon. This is done by taking a piece of lead and making a depression in it the size and shape of the bowl required. A piece of hard wood is shaped on the end grain to fit the depression made in the lead. The metal is placed over the depression and the wood shape placed on top of the metal; it is then driven into the form by using a hammer. This will give the general shape of the bowl which may be trued up later by sawing and filing.
[Ill.u.s.tration]
[Ill.u.s.tration: PLATE 48. SPOONS]
[Ill.u.s.tration: PLATE 49.
SUGAR TONGS AND TEA SCOOPS]
RIVETS.
The making of rivets is quite important as it is impossible to find in the market the variety in size and shape of head that each piece of work demands. Where rivets with a wire 1/8" or less are needed, they may be made as follows: Take a piece of iron or steel A, Plate 50, thicker than the desired length of the rivet and drill a hole through it having its diameter a little greater than the wire of the rivet. Take a piece of copper wire of the required diameter and about 1/8" longer than the thickness of the iron. Place the wire in the hole and the iron on some smooth metal surface, B. With a hammer make a burr of the wire that projects above the iron. Then reverse the iron and drive out the rivets.
This gives what is shown at D. The rivet is then cut off the required length, placed in position and headed up. The head may be made conical, I, hemispherical, J, pyramidal, K, or square, L, in shape. It may be headed up simply with the hammer, or with a rivet header, M.
When necessary, the process may be reversed and the head made first; but when made in this way, a rivet block is needed to rest the head in while making the burr.
The rivet may be made more of a decorative feature by sawing out of sheet metal some suitable design as shown at P, Q, R. Drill a hole in the center the size of the rivet and then use any ordinary rivet head.
Nails may be made by the same process, headed and pointed as at S and O.
[Ill.u.s.tration: PLATE 50. RIVETS]
TO DRAW WIRE AND SMALL TUBING.
[Ill.u.s.tration: FIGURE 30.]
[Ill.u.s.tration: FIGURE 31.]
Cut a piece of copper the length required, having the width about three times the diameter of the tube that is to be made. The edges must first be made parallel by filing. In a block of maple or some hard wood, with a wood file, make a groove as shown at Figure 30. Place the strip of metal over the groove and, with a somewhat pointed hammer, drive the metal into it until it takes the shape of a V. Figure 31 A. Then place it on the flat part of the block and strike on the edges with the hammer, turning them in until they meet, as at B and C.
[Ill.u.s.tration: FIGURE 32.]
A draw plate is then placed in the vise, Figure 32. After pointing the tube a little, the end is placed in one of the larger holes and drawn through. This will bring it somewhat into shape. Repeat this operation by drawing the tube through the hole the next smaller in size and so on till the tube is of the diameter required.
Wire may be drawn in the same way. Rectangular, triangular and square drawplates may be obtained as well as circular ones.
POLISHING.
To polish work, a cloth or felt buff is placed on a lathe or a polishing head. With a little cut-quick and rouge objects may be brightened by holding them against the wheel.
STAMPING WORK.
[Ill.u.s.tration: STAMP
FIGURE 33.]
The marking of work so that it will be known to whom it belongs and doing it in a neat and workmanlike manner is sometimes a problem. Using a gummed label with the name written on it has been tried, but the labels frequently come off. The name has been scratched with a sharp-pointed tool, but it is not an easy thing to do and certainly does not look well. The way described below however has proved very satisfactory. Have each pupil design a little trade mark of his own, and work it out on the end of a piece of tool steel, 1/8 inch or 3/16 inch square, round or hexagonal. This can be done by a little filing, perhaps the use of a drill if the design should call for it, and a little emery paper to take off all sharp edges. This serves as a stamp with which he may mark all of his work. The instructor has a book with the names of the pupils, and after each name he may stamp this mark and thereby register it so that he may tell at any time to whom work belongs.
Figure 33 shows a stamp and a few suitable designs.
COLORING.
The most satisfactory color that can be given copper is a bronze which comes naturally if left to come in contact with varying atmospheres. If the object has a good polished surface in the first place the color seems to become richer as time goes on.
A color that is satisfactory in many cases is obtained in the following way:
Place in a porcelain dish and bring to a boiling heat, liver of sulphur, 1 oz., and water, 1 qt. Dip the object to be colored in this solution while hot and then rinse in clean water. This gives the object a very dark color. Take a little powdered pumice stone on a piece of cloth and rub over the surface lightly bringing the copper color to the surface where desired.
A greenish color is given copper by submitting the object to the fumes of spirits of ammonia.
Beautiful colors are obtained by heating the object to different degrees, over a gas plate, but these results are not permanent.
Chapter X.
ENAMELING.
Enamel may be applied to metal objects and add a great deal to their value and attractiveness if used sparingly. The enamels most used are transparent and opaque; the transparent reflects the color of the metal adding a great deal of life to the work, the opaque gives color on the surface only.
The process, as described in this chapter, touches but the elementary stages of the art that are within the possibilities of high school work and possibly the upper grammar grades.
Enamel may be applied by any of the following methods:
First: By covering the entire surface of the object with enamel.
Second: By using a flat wire which is bent into sections the shape of the design and soldered to the object; the wire forms part.i.tions to receive the enamel.
Third: By cutting away the design by the use of engraving tools, making channels about 1/32 of an inch deep to receive the enamel.
Fourth: By using a chasing tool either from the front or from the back of the work, forming raised or sunken part.i.tions to receive the enamel.
The first and second methods are difficult ones, requiring a great deal of experience in handling metal and enamel to obtain satisfactory results.
The third and fourth methods are comparatively simple and are within the possibilities of those for whom this book is intended.
In the third method the design is first transferred to the object by the use of carbon paper and then made more permanent with a scratcher. The design is cut out with the engraving tools, Figures 6, 34 and 35, about 1/32 of an inch deep. All edges should be kept as smooth as possible and the channels should be uniform in depth. For convenience in holding, if the work is small, it may be fastened to a little pitch or wax spread on a block, or it may be placed on the pitch block as described under embossing on page 64. The handle of the tool is held in the palm of the hand, and the thumb, placed within an inch of the point, serves as a guide while cutting, Figures 34 and 35. By wriggling the tool a little from one side to the other, greater progress is possible.
0 Response to "Part 6"
Posting Komentar